Efficient processing principle: rolling technology, the application of the deep hole processing is a machining process, the roll flaking machine light is the ordinary deep hole with 2-3 times lawful to finish the work, once finished, the rough boring and fine boring and soluble in an organic whole, a complete USES push boring and coarse to fine boring, boring after using the timing of the return after complete rolling this procedure at the same time. 2, cutter tooth specifications selection principle cutter tooth specifications are mainly based on the cutting load borne by the cutter tooth in the cutting process to choose, and the cutting load is related to the cutter tooth width, the width of the cutter tooth should be allocated according to the cutting state of the cutter tooth and the size of the diameter of the drill bit.
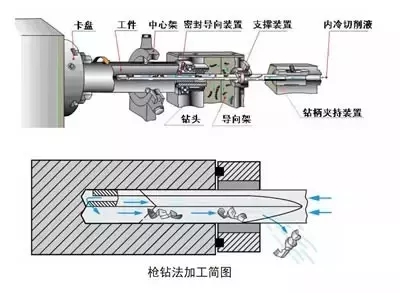
Is the ordinary deep hole with 2-3 times to complete the order of the work, once finished, the rough and fine boring dissolved in one, the use of push boring a complete rough and fine boring, after boring the use of the opportunity to complete the rolling process. The inner hole surface can reach the required surface roughness through attribute deformation. 1, cutter tooth material selection principle Cutter tooth material should be selected according to the load and cutting state of each tooth. The center tooth is subjected to the larger axial force, the extrusion friction is serious, and the cutting conditions are bad. Therefore, YG or YW cemented carbide blades with high bending strength and good impact resistance should be considered. And the outer tooth and middle tooth due to high cutting speed, should choose the red hardness, high wear resistance of YT class alloy, guide block should choose high wear resistance of YT class material. For general alloy steel processing, all cutter tooth material should be a comprehensive material, currently using YT798. 2, cutter tooth specifications selection principle cutter tooth specifications are mainly based on the cutting load of the cutting process of each cutter tooth, and the cutting load is related to the width of the cutter tooth, the width of the cutter tooth should be allocated according to the cutting state of each cutter tooth and the size of the diameter of the drill bit. The distribution of cutter tooth width should meet three conditions: a. Ensure drill tip eccentricity E =(0.1~0.2) D0. The e value is related to the material being processed and the diameter of the drill bit, and its size determines the size and direction of the radial resultant force of the drill bit. A reasonable amount of eccentricity makes a moderate radial force press on the machined hole wall, which can stabilize drilling, strengthen guiding and improve hole surface quality. At the same time, the zero cutting of drill tip is avoided, and the harsh cutting conditions at drill center are improved. B, A + C + e + F> D0/2 +(1~2)mm, that is, there must be a certain amount of overlap between cutter teeth; C, A + c – e – F> (1~3)mm, which can make the cutting radial force always pressure to the guide block, the guide block close to the processed hole wall forward, make full use of the guide block’s guiding role, to ensure the straightness of deep hole drilling. 3, the tool Angle selection principle deep hole processing tool Angle is mainly based on the workpiece material. Proper tool Angle is a great help in ensuring stability, chip breaking and tool durability during drilling.